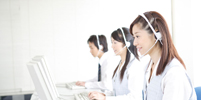
泊头市申泰量具厂
销售总机:0317-5560000
公司电话:0317-5560000
7*24服务热线:13833711135
公司传真:0317-7870444
公司邮箱:bt0317@163.com
公司地址:河北省泊头市工业开发区
华东地区:13131772330
华南地区:13131772331
华西地区:13131772339
华北地区:15720440949
- 划线平台铸件采用真空低压铸造的优点有哪些? [2013-12-12]
真空低压铸造法是在加压充型的过程中对铸模抽真空,充型完后保压使铸件在恒定压力下结晶凝固,铸件得到充分补缩,因而划线平台铸件组织致密,力学性能提高。此法多用于Al,Mg合金铸件的精密铸造。
真空低压铸造其优点如下:
1、一般情况下不需要冒口,使金属液的成品率大大提高,通常可达90%。
2、工作环境好、设备简单,有助于机械化和自动化。
3、真空低压铸造可以在低温时加快铝合金的流动性,避免高温浇铸造成的铝合金吸气现象,而增大了铸件的针孔缺陷。
4、铸件成形性好,有利于形成轮廓清晰、表面光洁的铸件及大型的薄壁铸件。
5、铸件组织致密,机械性能高。
6、适度提高真空度,使充型时间变短,不但充型速度加快而且平稳。
7、真空负压的存在,可以使模砂得到紧实,增大铸模的强度
- 在焊接平台铸件压力铸造过程中,选择的填充速度不宜太大或太小,怎么选? [2013-11-29]
在焊接平台铸件压力铸造的过程中,金属液的压力作用下,通过内浇道导入压铸型型腔的线速度,称之为填充速度,也称为导入速度,以m/s表示。它与压射比压一样,是压力铸造工艺的主要参数之一,对于轮廓清晰,表面粗糙精度细的铸件有着重要的作用。
在压力铸造过程中,填充速度的调节一般用调整压射冲头速度来实现。此速度不宜太大或太小,若填充速度太大,会使铸件产生气孔等缺陷;若填充速度太小,易使铸件轮廓不清。填充速度的选择应视铸件大小、复杂程度、铸件的要求、合金种类、压射比压高低而异。例如,对简单厚壁铸件,以及对铸件内部组织要求高时,应选择较低的填充速度和高的压射比压;而对薄壁复杂铸件或对表面质量要求高的铸件,应选择高的填充速度和高的压射比压,因为这时铸件成型是主要矛盾。压力铸造过程中常用的压射速度和填充速度,可参见表5. 4-25和表5.4-26选择。
- 在设计焊接平台压铸型时,不应忽视压铸型外形尺寸和压板厚度的设计,怎么办? [2013-11-25]
在设计压铸型时,人们往往只注意直接影响焊接平台铸件质量和尺寸精度的浇注系统及成型部分的设计, 而对压铸型外形尺寸和压板厚度的设计等却有疏忽。因此,时常有由于压板强度不够引 起变形而严重影响铸件尺寸精度,或者由于压铸型外形尺寸与压铸机规范不符等问题,妨碍压铸生产的正常进行,以致转化为生产中的主要矛盾。
由此可见,压涛型的外形尺寸和压板厚度的设计也是压铸型设计工作中的一个重要环节,在设计时应考虑到以下下几点:
a)能将压铸型吊装在压铸机上,并能牢固地压紧;
b)动、定型均应有适当的厚度,一般在较厚的情况下压铸型的温度变化下,铸件质量稳定,压铸型寿命也长,但压铸型太厚也不好,会使压铸型苯重,压铸机所受负荷加大;
c)压铸型的受力中心应尽可能接近压铸机上安装板的中心,否则压铸型不易闭合紧密;
d)压铸型各部分均应有足够的强度,以保证在高温、高压下不变形;
e)在型块周围到型块座板(亦称模板或模框)边的型面上,要有足够的位置来安装反推杆、导柱、导套、紧固螺钉及推杆导柱等;
f)在动、定两半型上都应有吊装螺孔;
g)推杆板的长度、位置应与压铸机的规格或附件相匹配。
为满足上述要求,压铸型外形尺寸可参见表5. 4-14,压铸型动型压板厚度可参见表5.4-15。
- 设置焊接平台压铸件浇注系统是应注意什么? [2013-11-22]
在压力铸造生产中,产生的废品很多是由于浇注系统设计不当造成的,因此浇注系统的正确设计时稳定压力铸造生产,提高焊接平台铸件质量的关键问题。
浇注系统不仅是液体金属填充压铸型的通道,还对金属流态,速度和压力的传递以及排气条件,压铸型热平衡等因素有调节作用。所以设计压铸件浇注系统,必须认真分析铸件的结构特点,技术要求,合金种类及其特性,还要考虑压铸机的类型及其特点,只有这样才能设计出合理的浇注系统。
通常,设计压铸件浇注系统时应遵循下述原则
a)提供稳定的金属流;
b)对金属液的流动阻力要小;
C)金属液流动时包卷气体要少;
d)对型腔的热平衡提供良好的条件;
e)使浇道内的金属液有适宜的凝固时间,既不妨碍压力的传递,又不增长操作循环时间;
f)造成的金属回炉料要少;
g)浇道的设置对铸件不应造成收缩变形;
h)在要求较高而又不允许加工的面上,不应设置浇道;
i)压铸件内有镶铸件时,浇道不应离镶铸件太远,以免金属液流到镶铸件附近时已降低温度,不能稳固地包住镶铸件;
J)浇道的清除工作应简便和不损坏铸件。
- 金属型铸造时的划线平台铸件脱型时间不宜太晚或太早,怎么办? [2013-11-11]
从浇注完毕到从金属型中取出划线平台铸件的时间(即铸件脱型时间),主要取决于铸件的大小和壁厚,并通过实验来确定,不宜太晚或太早。如果铸件脱型时间太晚,铸件脱型温度就越低,铸件收缩受阻就越大,对于金属芯及金属型型腔凸出部分的包紧力也就越大,拔芯及取出铸件也就更困难,甚至会造成金属型打不开及金属芯抽不出的现象。因此,一般希望尽早脱型,这样铸件收缩小,产生内应力和裂纹的倾向小,对铸铁件还能避免形成白口层。但是,脱型时间不能太早,否则铸件强度会低,容易变形损坏。
通常,对非铁合金铸件,一般的经验是,当浇冒口基本凝固完毕,即可抽芯开型,铝合金铸件脱型时的平均温度约为450~5000C,镁合金铸件脱型时的平均温度约为350~4000Co对一般铸铁件,则掌握在温度为9000C时即可开型;对薄壁铸铁件,为防止白口,开型时间可更早些,可控制在900~9500C时开型,铸件取出后应进行保温暖冷,或利用余热进行正火处理。
- 为什么金属型铸造划线平台铸件时不应忽视对金属型型腔和浇冒口处喷刷一层涂料? [2013-11-08]
金属型铸造划线平台铸件时不应忽视对金属型型腔和浇冒口处喷刷一层涂料,因为它是获得金属型优质铸件和延长金属型使用寿命的重要环节。
金属型铸造时,对金属型型腔和浇冒口处喷刷一层涂料的主要作用是:
a)减低高温液体金属对金属型的“热击”作用,减少金属型型壁的内应力,因为金属液充满型腔的时间只有几秒到几十秒钟,在这样短的时间内,金属型工作面如不喷刷涂料,则来不及把热量传到型壁整个断面上,型壁内外温度差很大,产生很大的内应力,甚至可能引起金属型裂纹,但涂料层导热能力差,可削弱型壁受热的剧烈程度,起到对金属型的保护作用;
b)耐热的涂料层把液体金属和型壁间隔开来,避免铸件和金属型壁发生熔焊现象,保护金属型不被烧伤,延长金属型寿命:
c)对金属型不同部位(例如型腔、浇冒口),喷刷不同成分的涂料,并控制涂料层的厚度,就能根据需要使铸件按规定的方向顺序凝固,以便于在铸件最后凝固的地方安置冒口,并能提高冒口的补缩能力;
d)涂料层能减少型壁对液体金属的摩擦阻力,有利于液体金属的流动,改善充填金属型的能力;
e)涂料层有一定的排气能力;
f)使铸件表面光洁,并易于脱型;
g)对铸铁件,涂料层能减少和避免表面白口。
- 生产焊接平台铸件设计金属型时不应忽视排气系统,那么应怎样设计? [2013-11-04]
生产焊接平台铸件设计金属型时,不应忽视排气系统,因为制作金属型的材料本身没有透气性,而且如果排气系统设计不好,还会使铸件产生冷隔、浇不足、外形轮廓(花纹字迹)不清晰、气孔等缺陷对于有色合金,因其表面氧化膜厚,表面张力大,更容易形成轮廓不清晰的缺陷。
通常,设计金属型的排气系统时应注意以下几方面:
①在确定焊接平台铸件在金属型中的位置并拟定浇注系统时,必须要考虑金属液的充型过程,使其有利于将型腔中浇注时卷入的和挥发物所产生的气体排出。
②如果铸件上部无需安置冒口,但最好也应开设排气冒口或排气孔。暗冒口的顶部也应设计排气孔。排气孔一般开设在金属型的最高处或金属型内可能产生“气阻”的地方(如图5. 3-6所示),其直径为¥1~5mm或宽为2~
3mm、长为15~20mm,并直接通至金属型外部。
③金属型上与型腔连通的各配合面(如芯座、活块、顶杆与型体的配合面)以及金属型分型面上也可开设排气槽。排气槽又称通气槽、通气沟等,要求即能迅速排出型腔中的气体,又能防止液体金属浸入。故根据不同合金,排气槽的深度应有一定限制,扁缝形排气槽的深度,对铸铁和青铜一般为0. 25mm,对铝、镁合金一般为0. 5mm,间距口为10~15mm。三角形槽深度h-般为0.3~1.Omm,间距口取lOmm。排气槽的结构形式可参考图5. 3-7。
④在金属型型腔的凹处以及个别凸起 图5. 3-7金属型排气槽的结构形式部位可钻孔,装进排气塞,以利排气。排气塞又称通气塞,可用45钢或铜棒制成。金属型常用排气塞的结构如图5. 3-8至图5.3-10,A型排气塞的尺寸见表5.3-13。
⑤金属型上开设排气系统的截面积,原则上应等于或大于金属型浇注系统的最小截面积。
⑥金属型排气系统的设置应不影响开型及抽芯。
此外,还可考虑通过砂芯和壳芯排气,利用涂料层排气以及设置抽气装置进行人工抽气。
- 为什么金属型铸造钢铁铆焊平台铸件时不宜使用金属芯? [2013-10-24]
金属型铸造铆焊平台铸件中,一般应尽可能使用金属芯,并避免使用砂芯,因为使用金属芯有如下优点:
a)生产率高,操作方便;
b)尺寸稳定,减少零件加工余量,节省金属,
c)加速铸件的冷却,并能得到细小的晶粒组织,提高铸件的力学性能,同时也能减少一部分铸造缺陷,
d)便于抽芯机械化、自动化;
e)避免了砂处理工作,省去了砂处理设备,便于组织生产,节省车间面积。
但是,如果铸件内腔过于复杂,不能或不易从铸件中抽出金属芯时,则不可避免地要使用一部分砂芯,或全部使用砂芯。特别是,对于金属型铸造黑色金属铸件时,则更不宜使用金属芯,而应普遍使用砂芯。因为黑色金属(如铸铁、铸钢)的熔点高,若使用金属芯,由予型芯膨胀很大,很难从铸件中抽出,并容易造成铸件裂纹等缺陷,甚至会造成金属芯与铸件熔接的现象,因而影响着正常生产的进行。
- 确定焊接平台铸件在金属型中的分型面时应注意什么? [2013-10-21]
选择焊接平台铸件在金属型中的分型面是设计金属型结构的最重要条件之一,它应和确定铸件在金属型中的浇注位置同时进行。铸件分型面一般有垂直、水平和综合分型(垂直、水平混合分型或曲面分型)三种。
一个铸件经常有几种分型的可能,选择分型方案时,必须从多方面比较,找出最合理的方案。通常,选择铸件在金属型中的分型面时应注意以下九点:
①选择的分型面应保证金属型能顺利开型和取出铸件,不允许损坏金属型或铸件。
②为简化金属型结构,提高铸件精度,对形状较简单的铸件最好布置在半型内,或大部分布置在半型内。
③为保证铸件外形美观,分型面数目应尽量少,最好是平面分型,这样便于金属型的加工和检查尺寸,由于两半型能准确地吻合,可使铸件尺寸精确,金属型制造简单。
④为有利于采用良好形式的浇注系统和安设胃口,为有利于排除型腔中的气体以及使金属型操作方便和易于机械化,最好采用垂直或互相垂直的分型面。
⑤也可考虑采用折线面作为分型面,并应尽量避免采用曲面分型。如果由于铸件形状的原因,曲面分型不可避免,则必须保证分型面成规则的几何形状。对复杂的曲面,可将铸件以不显著的局部失真,或者用局部镶嵌件来改成折面。
⑥选择分型面时,应使金属型尽量少用拆卸件及活块,因为这类零件过多会使金属型制造复杂,缩短金属型使用寿命,降低生产率,同时也影响铸件的精度和美观。为了避免这些缺点,在某些情况下增多分型面或采用折面分型较为有利。特别是采用金属型铸造黑色金属时,拆卸件和活块损坏很快,更不宜采用。
⑦选择分型面时,应尽量使型芯数量少。若必须采用砂芯,则应使砂芯安装方便,定位准确,固定牢靠。
⑧选择分型面时,应使铸件的基准面和大部分加工面在同一个半型内,分型面不得选在加工基准面上。
⑨分型面的选定,应使金属型型腔内涂料层喷刷、修整方便,金属型在工作过程中涂料层不剔损坏。
- 进行金属型铸造的焊接平台铸件图设计时,应怎样选择铸造的基准面? [2013-10-17]
进行金属型铸造的铸件图设计时,首先应考虑的是确定焊接平台铸件的铸造基准面,因为它决定了零件各部位相对的尺寸位置,因此在选择铸造基准面时不能与铸件机械加工的加工基准面相矛盾,而应保持统一。
通常,在选择铸件的金属型铸造基准面时,应注意以下几点:
①非全部加工的铸件,应尽量取非加工面作为基准面。因为加工面在加工过程中,,尺寸会因加工公差而变动,这样将影响相对尺寸位置的变动,并且铸件经过加工后,到底加工去.掉多少余量不好检查。
②采用非加工面作基准面时,应该选尺寸变动最小的,最可靠的面做为基准面,但是,用活块形成的铸件表面最好不选为基准面。
③基准面应尽可能平整和光洁,不应当有浇冒口的残余、毛边等。
④全部加工的铸件,应取加工余量最小的表面作为基准面,这样保证机械加工时不致因加工余量不够而造成废品。
⑤为了检验尺寸方便,最好是选取较大的平面作为基准面,尽量避免取弯曲的面,或是有铸造斜度的面。
- 采用陶瓷型铸造生产铸钢件时,不应忽视检验平台铸件表面脱碳问题,怎么办? [2013-10-14]
采用陶瓷型铸造生产铸钢检验平台铸件时,不应忽视铸件表面脱碳问题。通常,在合箱前,应在陶瓷型型腔表面薰上一层薄薄的乙炔炭黑,或喷上一层树脂溶液,或在氮气保护下浇注,可以有效地防止或减少铸钢件表面的脱碳,还可防止铸钢件表面形成氧化铁皮和粘砂。
- 设计陶瓷型铸造的焊接平台铸件浇冒口系统时应注意什么? [2013-10-10]
陶瓷型铸造常用来生产各种模具和复杂的焊接平台铸件零件,在设计陶瓷型铸造的浇冒口系统时应注意三点:
其一是,陶瓷型极容易吸附金属液中的酸性熔渣,对于易氧化而熔渣多的合金,应尽量选用挡渣效果好的浇注系统;
其二是,内浇道不应设置在铸件的重要位置.,因为内浇道外的陶瓷型容易过热,而导致铸件晶粒粗大,或出现缩松等铸造缺陷;
其三是,冒口不仅应起到补缩作用外,还应具有制造简单、排气顺畅和合型浇注方便等优点。
通常,陶瓷型铸造的浇冒口系统可参见表5.2~6选用
- 设计焊接平台使用的陶瓷型铸造的母模时,不应忽视母模的表面粗糙度,那么应怎样考虑? [2013-09-30]
设计焊接平台使用陶瓷型铸造的母模时,不应忽视母模的表面粗糙度,因为它直接影响着陶瓷型的表面质量,也直接影响着陶瓷型铸件的表面质量。表5. 2-2是不同粗 表5.2-1复合陶瓷型表层糙度母模对陶瓷型表面质量的影响情况。
为了铸出表面光洁的陶瓷型焊接平台铸件,必须保证具有光洁表面的陶瓷型和母模,其办法通常有二:
一是选择适宜的母模材料。陶瓷型母模材料有:木材、石膏、环氧树脂、塑料和金属等,可根据铸件的表面质量、尺寸精度、产量和形状复杂程度等选择,井参见表5. 2-3。
二是选择合适的分型剂,目前广泛采用的分型剂有:上光蜡、变压器油、黄油、硅油、树脂漆和聚苯乙烯液等,其中以聚苯乙烯液的涂覆性能和表面光洁效果最好,可参见表5. 2-4至表5.2一5。
- 焊接平台铸件制造熔模铸造硅溶胶粘结剂型壳时应注意什么? [2013-09-26]
制造熔模铸造焊接平台铸件硅酸乙脂粘结剂型壳时,与制造硅酸乙脂粘结剂型壳一样,也应从以下六个方面引起注意:
(1).在涂料配制方面的注意点 硅溶胶常用水玻璃经阳离子交换树脂去掉钠离子,再经阴离子交换去掉氯离子和其他杂质,然后用常压或真空浓缩而制得,是一种高度分散Si0。颗粒的水基聚合胶体溶液。熔模铸造用硅溶胶的质量分数一般为300。配制涂料前,通常对购进的硅溶胶需用乙醇或水进行稀释处理,使WSi0。降低20~0~24%,粘度≤8×10-8Pa.S,用乙醇处理硅溶胶,不但起稀释作用,|同时也能降低胶液的表面张力,改善涂料的涂挂性能,加速涂料层的干燥速度。配制涂料时,主要是控制涂料的密度和粘度,除加入稀释后的硅溶胶和耐火粉料外,尚需加入一定量的表面活性剂(如JFC或EA)和消泡剂(如正辛醇或乙二醇丁醚磷酸脂等)。
(2)在模组除油与脱脂方面的注意点(可参见本章第1 3条(2)
(3)在涂挂涂料与撒砂方面的注意点(亦可参见本章第1 3条(3)
( 4)在硅溶胶型壳干燥与硬化方面的注意点 硅溶胶粘结剂涂料层的干燥.实质上是硅溶胶的胶凝过程,但水分蒸发在先,胶凝在后。因此,在干燥过程中应控制良好的外部条件,使型壳中大部分水分在尽可能短的干燥时间内通过型壳表面蒸发而排除,外部的干燥条件主要包括:温度空气相对湿度和空气流速’加速干燥过程的方法有。强制通风干燥、静电干燥、真空干燥以及远红外射线加热干燥等。
- 金属液浇入型壳后,为什么焊接平台铸件的脱壳时间不宜过早或太迟? [2013-09-23]
金震液浇入型壳后,焊接平台铸件应等待一段时间再进行脱壳,不宜过早或太迟。如果铸件脱壳过早,会使铸件产生过大的内应力而发生变形或裂纹;如果铸件脱壳太迟,则会使某些碳含量高的铸钢件易产生较厚的脱碳层,而影响铸件表面质量。
铸件的脱壳时间,即铸件的冷却时间长短取决于铸件的材质、形状、尺寸和生产条件。通常,含合金的焊接平板铸件或易产生变形、裂纹的材质和形状的铸件,其冷却时间应长些;而对薄壁小件,其冷却时间则可短些。但应注意的是,无论哪种合金,都应保证铸件在脱壳时的温度要低于该合金的相变温度,一般碳钢铸件宜在600~650度温度下脱壳,合金钢铸件一般应降蛰soooc以下进行脱壳,对于结构复杂的合金钢铸件要降到200摄氏度以下才能脱壳。
- 焊接平台使用的易熔模出现缺肉的产生原因及控制方法 [2013-09-19]
焊接平台使用的易熔模出现缺肉的产生原因:
1.模料流动性差
2.模料压注温度或压型温度低
3.压注压力小或压注速度太慢
4.压型注射口太小或位置不当
5.压型型腔排气不良
6.模料注入量不足
防止方法:
1.改进模料,提高模料流动性
2.提高模料压注温度和压型温度
3.增加压注压力或增加压注速度
4.扩大压射口或调整注射口位置
5。改善排气口条件
6.增加模料注入量
- 焊接平台使用的低温模料的特点及其选用范围 [2013-09-16]
焊接平台使用的低温模料的特点:
1.是以各种矿物螬和动、植物螬为主体的模料,常用的是以石 蜡-硬脂酸为基的模料。为改善其性能,可在该模料中适当添加其他组元,例如地螬、蜂蜡、褐煤螬、聚乙烯、低分子聚乙烯、乙烯一醋酸乙烯酯共聚物、松香和乙基纤维素等。也可以石蜡为基添加其他组元.常用低温模科配比及其技术特性,可参见表5. 1-4和表5. 1-5.一般膏状压制,可用热水脱蜡 5. 1-5.一般膏状压制,可用热水脱蜡.
2.熔点低于70*C,强度较低,热稳定性差,收缩大,易熔模尺寸形状随室温变化较大,表面粗糙度较高,但生产工艺简单,模料回收率高,可重复使用,成本较低.
选用范围:适用于制造尺寸精度不高和表粗糙度要求不太低的小型易熔模.
- 焊接平台铸件设计制造熔模铸造用石膏压型时应注意什么? [2013-09-13]
焊接平台铸件石膏压型是利用石膏浆料经灌注、凝结后制成的。通常,在设计制造时应注意以下五点:
①石膏易碎,切忌局部受力过大,夹紧时应有较大的接触面。
②对于较大的石膏压型,其中应有金属骨架或加设金属加固框。
③对于形成易熔模内腔的型芯,最好采用金属芯,以保证型芯的良好导热,型芯的导向部分应镶人金属构件。
④为了改善透气性,应在分型面上刻出深0.3~0. 5mm的排气槽。
⑤压型的定位应采用金属定位销和销套,石膏定位榫。
- 进行焊接平台铸件熔模铸造工艺方案设计时,铸件基准面应怎样选择? [2013-09-09]
进行铸件熔模铸造工艺方案设计时,焊接平台铸件基准面一般选择在非加工面上,且应是尺寸比较稳定的平整光洁表面,而不应有浇冒口残余、毛刺和斜度等。若需选择在加工面上时'最好也是加工余量较少的面。
通常,铸件上的外圆、平面、内孔和端面都可以作为基准面,其数目一般为三个(回转体零件可选择二个),能约束六个自由度,并力求划线与加工为同一基准面。
- 铜焊接平台铸件热处理出现翘曲和变形的原因与防止方法 [2013-09-05]
铜焊接平台铸件热处理出现翘曲和变形的原因:加热和冷却速度过快,产生较大应力铸件装炉时,放置不合适。
防止方法:
1,调整加热和冷却速度;
2,调整铸件在炉中的安置方向或采用专用夹具。